配電盤類の板金加工は、抜き、曲げ、溶接からなります。
スポット溶接は、溶接速度が速く、自動化が容易であるなどの長所を有する抵抗溶接です。
スポット溶接の原理 と 溶接条件 について説明します。
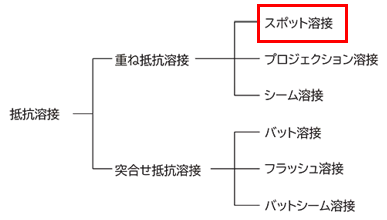
スポット溶接の 原理
●スポット溶接は、重ね合わせた2枚のワークを電極で挟み初期加圧します。
加圧状態で大電流を流し通電します。
電極とワーク、ワーク同士間に抵抗熱が生じ金属が溶けます。
保持加圧して冷却すると接合部に碁石状の溶接部(ナゲット)ができます。
⇒ ⇒
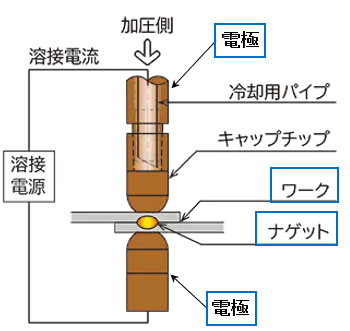
●ワークとワークとの間が発熱し金属が溶けますが、電極とワークは溶けません。
銅製の電極はワークと比べて電気抵抗が少なく( 銅:SPCC=1.7:15 )、
抵抗による発熱が少ないからです。
また、電極は熱伝導率が高く( 銅:SPCC=390:73 )、
電極先端から効率よく放熱でき、さらに水冷するので電極の温度が上昇しません。
従って電極とワークは溶着しません。
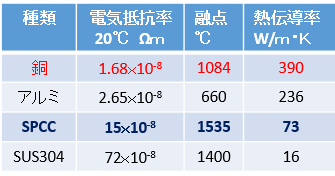
●溶接電流、通電時間、電極加圧力の3条件と電極管理が大切で、適切な組合せが重要です。
溶接電流・・・溶接材に流れる電流(アンペア)
通電時間・・・溶接電流が流れている時間
電極加圧力・・被溶接板(ワーク)に加える力
●スポット溶接の長所と短所
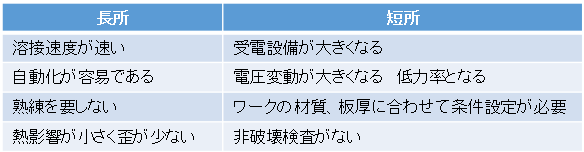
スポット溶接の 溶接条件
●スポット溶接条件は、RWMA(米国抵抗溶接機製造者協会)の条件表が有名です。
表を参考に溶接電流、通電時間、電極加圧力を設定します。
●RWMAの普通条件であるCクラスを下記に示します。
現場のナゲット径のバラツキは大きい。
クラスCのナゲット径は、電極先端径dより若干大きく、安定した溶接条件です。
電流を変えてナゲット径を調整するのは、発生熱量が電流の二乗に比例するため難しいため
一般的には時間でナゲット径を調整します。
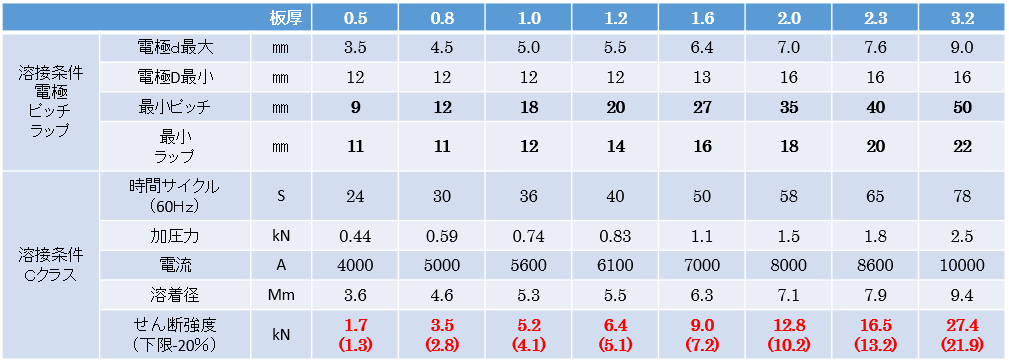
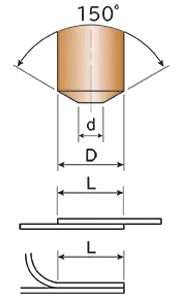
●最小ピッチは、分流を考えなくてよい「隣の溶接点との最小距離」です。
基本は最小ピッチ以上にし、これより短くなる場合は、分流効果による溶接不良を考慮して
選定してください。
●最小ラップは表のL寸法です。
Lをこの値以下にすると強度が低下し、ひずみが生じますので注意してください。
●溶接時間は電源周波数60Hzにおけるサイクル数です。(10サイクルは6分の1秒です。)
50Hzの電源で溶接する場合、溶接時間を本表数値の6分の5に変更してください。
●せん断強度は1点当たりの 強度です。
●板厚異なる2枚の板を溶接する場合は、薄い方の板厚に従ってください。
(但し板厚の比は、1:3以内で薄板側は凸電極の場合)
参考1:スポット溶接の用語
1)ナゲット
接合部に生じる溶融凝固した部分。
一般に接合面を中心とした碁石状の形状。
ナゲット径は碁石状の直径で、溶接の強度はナゲットの大きさによる。
2)コロナボンド
ナゲット周囲に生じるリング状の部分。
3)溶込み深さ
接合界面に対して垂直方向に計測した各板中でのナゲットの最大溶け込み量。
4)ブローホール
ナゲットの内部に生じる気孔。一般にナゲットの中央部に生じる。
5)中ちり
溶融金属がコロナボンドを破って外にでてくることをいう。
加圧力に対し溶接電流が多すぎる。
又は溶接電流に対し加圧力が小さい場合に発生。
6)ピット
くぼみに生じる表面に口をあいた深い穴
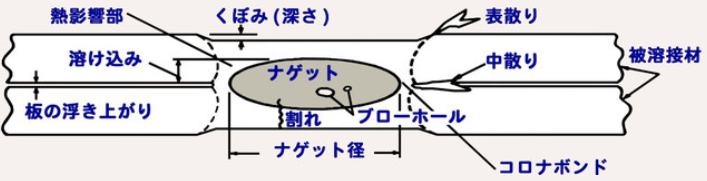
参考2:スポット溶接の溶接記号
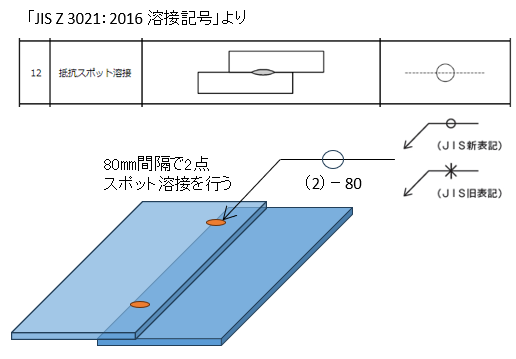
以上 最後までお読みいただき ありがとうございます。